Views
Investing in People, Not Just Technology
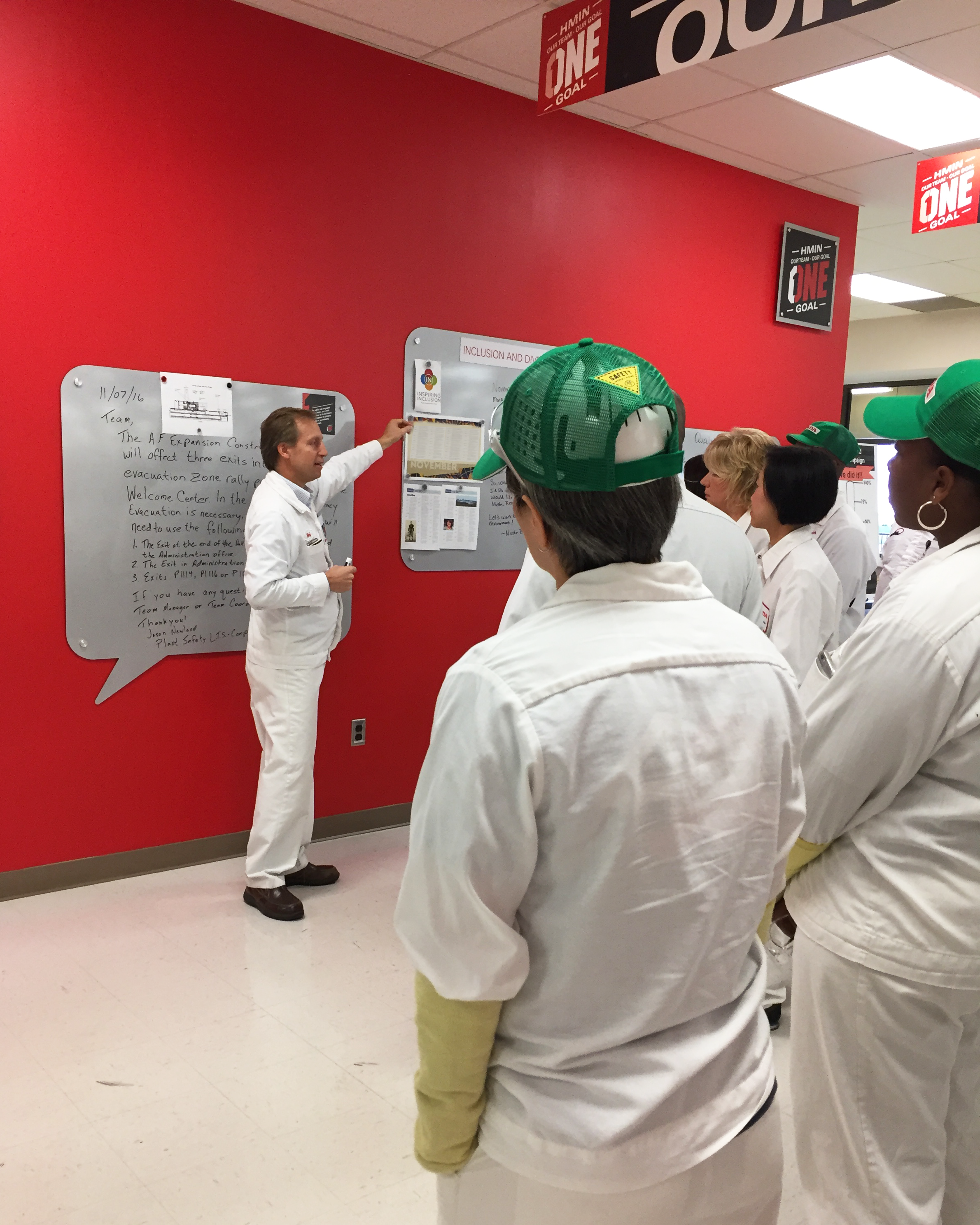
In manufacturing, there is always a new and better way to do things. Identifying what we can improve and working as a team to make that a reality has been our focus since Honda began building products in America in 1979.
The key to our success is "The Honda Way" – a culture based on teamwork, respect and open communication. From time to time, there are suggestions from outside the company that there is a better approach. Yet, over the past four decades, no automaker has been more successful than Honda in growing its production operations in America – starting from a single plant in Ohio to 12 plants in seven states employing almost 23,000 associates in production-related roles.
The Associate Voice
When I was leading our Indiana Auto Plant several years ago, I became passionate about listening to what we now call the "Associate Voice." The more we listen, the more valuable insights we will get, and the better our company and our products become.
When associates have concerns about a difficult production process or company policy, we not only want to hear about it, we want their suggestions for how to fix it and welcome their involvement in our efforts to improve.
One of the best examples occurred several years ago. We were contemplating a change in our production shift schedule. In Indiana, we followed a rotating shift schedule, where associates alternated every two weeks between the morning and afternoon production shifts. Our initial intention was fairness, but we found that most associates disliked alternating shifts. We needed to decide whether to move to a fixed shift schedule for all associates. What was unique is how we made the decision.
Traditionally, companies decide the work schedule. What we did was make every aspect of the change based on the Associate Voice – our process of listening to and communicating directly with our associates that is now utilized across every one of our U.S. production facilities.
We formed a team from each area of the company: including production associates, production managers and the company management team. Every team member, regardless of position, was equally responsible for understanding the project to be able to share information with other associates as the foundation for decision making.
Transparent Communications
We were transparent right from the start and established communication boards throughout the plant that contained the names of everyone on the team associates could go to with questions, as well as the project schedule and any weekly communications. We also did some other new things like establish our "Red Wall," visible to all associates, where we communicate not only what we are doing, but why. The messages are hand-written and signed by our leaders, with associates stopping to read these messages to create an informal, but important point of engagement.
We also shared detailed information about the shift schedule options every associate could choose from. Then we surveyed every associate about their preferences, enabling them to rank each option.
Decision-making Led by Associates
The most powerful moment for me was when it came time to announce the decision. It wasn't me informing our associates. Rather, an associate on the team stood up to inform top management what the new operating structure would be. We wanted our production associates to decide something as essential as when they show up to work every day.
But that isn't the end of the story. This approach we call the Associate Voice that began in Indiana is now an initiative across every Honda production facility in America. In fact, the team in our Alabama Auto Plant is in the midst of studying a possible shift change using the same process used in Indiana to make sure we're listening to our Associate Voice.
Honda associates contribute hundreds of suggestions to change the design of new products and the processes that will be used to build them. Some of the suggested changes take time to be acted upon. But even if we can't do it right away, or at all, we always try to explain why. As a former executive once said: "There is no graveyard for associate ideas." We don't know of another automaker where production associates have such a strong voice in new vehicle design or company policies.
Investing in Our Future
The key point in this story is not the shift change. Afterall, while the Honda Way is shared in all our operations, a policy that works for associates at one local operation may not be preferred in another facility. The hero of this story is the Associate Voice. What is important is that we listen to it and do our best to ensure that our policies and practices give our associates the best chance for success – at the plant and at home as well.
We will continue to invest in our people, listen to their ideas and work together to create products of the highest quality for our customers and maintain the unprecedented job security for our associates and their families.
That is The Honda Way.
Bob Nelson
Executive Vice President
American Honda Motor Co., Inc.
Error: You currently have access to a subset of X API V2 endpoints and limited v1.1 endpoints (e.g. media post, oauth) only. If you need access to this endpoint, you may need a different access level. You can learn more here: https://developer.x.com/en/portal/product